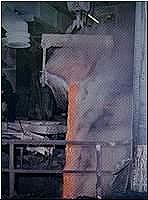 Poche de coulée à la
fonderie de Lubumbashi
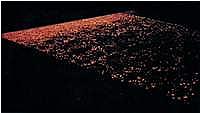
Tapis de
concentrés en cours de grillage et
d'agglomération sur machine Dwight-Lloyd aux
usines de Lubumbashi

Tuendeni kula
shaba
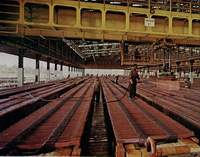
La salle
d'électrolyse de l'Usine de Luilu. Sous l'action
du courant électrique, le cuivre de la solution
se dépose sur les feuilles amorces (cathodes)
par l'intermédiaire d'une anode insoluble en
plomb antimonieux. En cinq jours environs, les
feuilles amorces plongées dans les cuves verront
leur poids passé de 4 à 50 kg.
|
Le schéma de
traitement (en fin de chapitre) résume mieux
quune longue description, la série
dopérations que subissent actuellement les
diverses catégories de minerais fournis par les
mines et carrières, depuis leur extraction
jusquà lobtention dun produit
exportable, que ce soit du cuivre, du cobalt, du
zinc, du cadmium, du germanium ou des métaux
précieux. En résumé, on peut
dire que nous utilisons actuellement deux grands
procédés de traitement: le traitement thermique
et le traitement électrochimique.
Les usines de
Lubumbashi emploient le procédé thermique;
elles traitent principalement les concentrés
sulfurés de Kipushi. Ces concentrés contiennent
trop de soufre pour être traités directement
aux fours water-jacket et donner une matte
(sulfure double de cuivre et de fer) à teneur en
cuivre satisfaisante.
Les concentrés fins ne
peuvent au surplus être chargés tels quels dans
les fours, et doivent être agglomérés. En
quelques mots, avant dêtre fondus, les
concentrés sulfurés de cuivre doivent subir une
double opération: lagglomération et le
grillage. Ce sont des appareils Dwight &
Lloyd qui assurent cette double fonction. Par
combustion, une bonne partie du soufre est
éliminée et les fumées sulfureuses sont
rejetées dans latmosphère par la
célèbre cheminée de Lubumbashi.
Les agglomérés
auxquels on ajoute éventuellement les
concentrés oxydés pour obtenir un rapport
convenable entre les teneurs en cuivre et en
soufre de la charge, sont enfournés dans les
water-jacket avec du coke, agent thermique.
A la température de
1300 degrés environ qui règne dans la zone de
fusion du four, la séparation se fait par
densité entre la gangue qui forme la scorie et
le cuivre qui est rassemblé dans une matte ayant
une teneur de 64 % de cuivre environ. La scorie
sécoule par un trou de coulée aménagé
au niveau supérieur du creuset; cette scorie est
alors granulée par un jet deau froide qui
lentraîne dans des bassins de décantation
doù elle sera évacuée pour être mise à
terril.
Le cuivre, en raison de
sa grande affinité pour le soufre, forme un
sulfure, principal constituant de la matte qui
saccumule dans le fond du creuset. Cette
matte est conduite par un chenal dans un four
dattente.
La matte est ensuite
traitée dans un appareil cylindrique rotatif
appelé convertisseur. Celui-ci « convertit »
la matte en cuivre par élimination du soufre et
dune bonne partie des autres impuretés
(fer, plomb, arsenic). Le cuivre métallique
obtenu est coulé en lingots de 140 à 180 kg.
Arrivé à ce stade, le cuivre brut ou « blister
» a atteint une pureté de 98,5 à 99 %. Il
devra avant dêtre utilisé subir un
raffinage. Ce raffinage est opéré à façon en
Europe, par voie électrolytique. Signalons enfin
que les poussières métallurgiques sont
soigneusement récupérées. Les gaz et fumées
dans lesquel elles se trouvent sont acheminés
vers une installation de dépoussiérage. Les
poussières contiennent principalement du cuivre,
du zinc, du plomb, du cadmium et du germanium.
Le
traitement électrochimique |
Les installations
hydrométallurgiques de Shituru et de Luilu utilisent
un procédé électrochimique. Ce procédé
consiste à dissoudre les minéraux de cuivre et
de cobalt dans lacide sulfurique dilué, à
débarrasser mécaniquement de sa gangue la
solution ainsi obtenue et à soumettre la
solution de sulfate la plus pure possible à
lélectrolyse. Les cathodes obtenues sont
fondues et le métal est raffiné thermiquement,
puis coulé en lingots marchands (wire-bars
principalement).
Le cuivre
Lixiviation
Dans les deux usines,
les concentrés oxydés sont déversés soit,
comme à Shituru, dans des « pachucas », cuves
cylindriques, soit, comme à Luilu, dans des
agitateurs de 120 m3 chacun. Les
concentrés sont maintenus en suspension dans une
solution sulfurique par un brassage à lair
comprimé, jusquà dissolution du cuivre et
du cobalt, tandis que les éléments de la gangue
qui ne sont pas attaqués restent à létat
solide. Une partie du fer est également dissoute
et pour maintenir une teneur convenable du fer
dans la solution, lexcédent est éliminé
au cours dune opération de « purification
fer ». Une partie de lalimentation des
usines est constituée par des concentrés
sulfurés que lon grille dans un four
fluosolid (grillage sulfatant). Transformés en
sulfates doubles de cuivre et de cobalt, ils
rentrent dans le circuit de lixiviation des
concentrés oxydés.
Electrolyse
La solution clarifiée
est envoyée à la section délectrolyse.
Sous laction du courant électrique, le
cuivre de la solution se dépose sur les feuilles
amorces (cathodes) par lintermédiaire
dune anode insoluble en plomb antimonieux.
En cinq jours environ,
les feuilles amorces voient leur poids passer de
4 à 50 kg. Les cathodes sont alors retirées des
cuves et remplacées par de nouvelles feuilles
amorces. Au sortir des cuves, la solution qui
sest progressivement appauvrie en cuivre et
enrichie en acide sulfurique, est renvoyée à la
lixiviation pour dissoudre dans les pachucas ou
les agitateurs une nouvelle quantité de
concentrés.
Raffinage
Les cathodes de cuivre
dont la teneur est de lordre de 99,4 % sont
raffinées dans un des trois fours à réverbère
de Shituru, les seuls actuellement construits au
Katanga.
Cela signifie que les
cathodes de Luilu ne sont pas raffinées sur
place. Elles subissent cette opération soit à
Shituru, soit en Europe.
Le cuivre
électrolytique est alors coulé en lingots. La
pureté de ce cuivre électrolytique dépasse
99,95 %.
Traitement
métallurgique suite->>
|